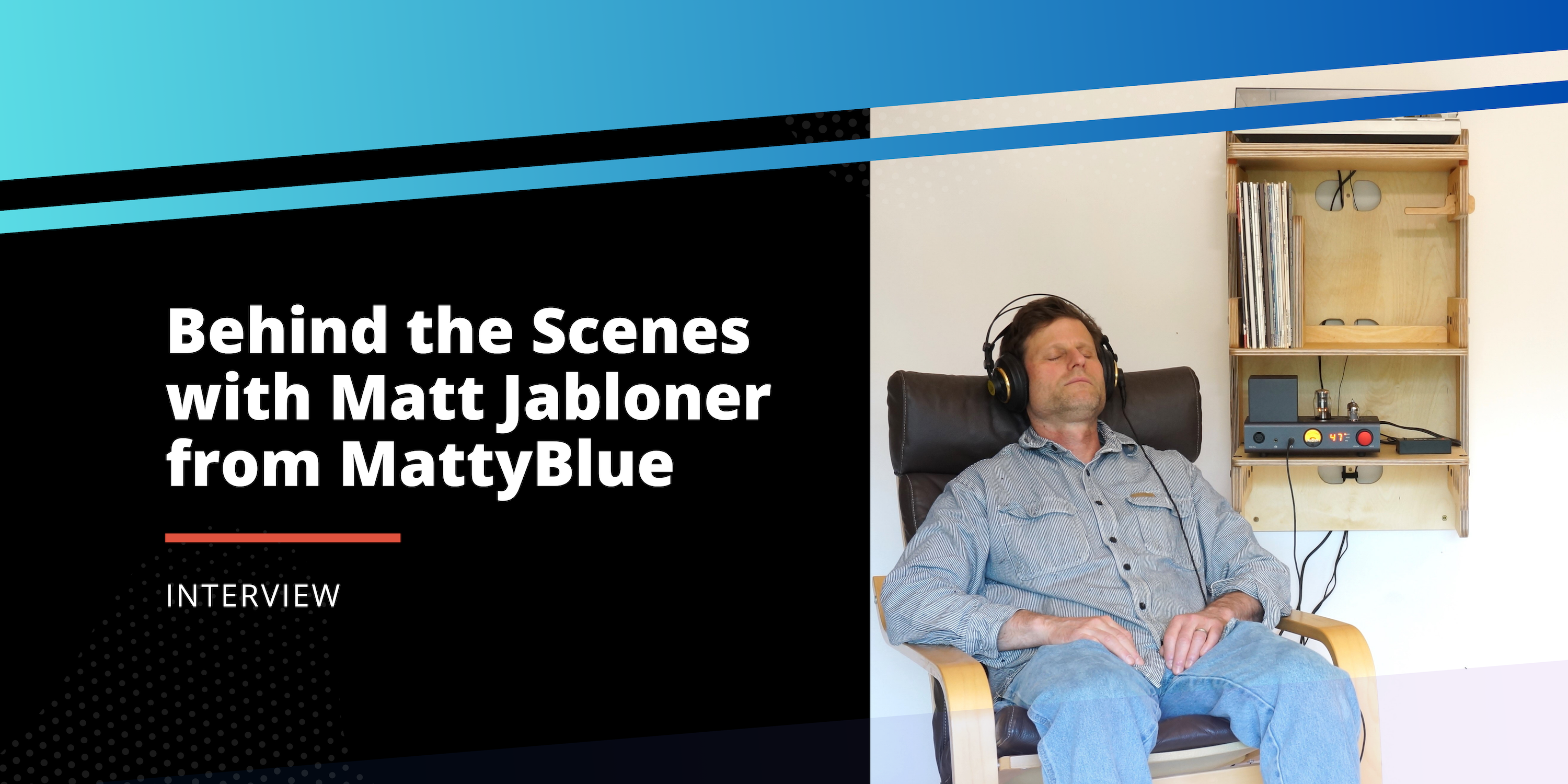
Behind the Scenes with Matt Jabloner: An Interview with Apos
Creating the Apos x MattyBlue Wall-Mounted Gear Rack
Tom from Apos here! In this behind-the-scenes interview, I caught up with Matt Jabloner to dig into the story behind the Apos x MattyBlue Wall-mounted Gear Rack. We cover everything from his lightbulb moment to the nitty-gritty of designing and the priceless—if, at times, ahem, honest—feedback from Apos 𝒙 participants.
How a lacrosse ball was the mother of invention
The idea for the wall-mounted rack hit Matt when he was working on a recent project for Bottlehead called Solitary Confinement. "I spent a huge amount of time with a vibration sensor, dropping a lacrosse ball on the floor adjacent to a test platform to measure the vibration response," he said. "After doing that for a while, it hit me just how bouncy floors can be. That’s when the idea struck—why not create a wall-mounted turntable rack? Wall-mounting reduces vibrations, and besides, I love how clean and elegant things look when mounted on a wall. Plus, it’s always great to have something beautiful on display."
Big, stable: prototyping the rack
Matt had two chief goals for the first prototype: size and stability. "It’s pretty large," he explained. "I wanted to make it big enough to hold a large tube amp since some of them can get quite tall and heavy. For the test, I mounted the rack to a stud and placed a 42-pound concrete block on it for half an hour."
His background in custom furniture played a major role in the design. "Years ago, I made custom furniture, including a wall-mounted cantilevered bookshelf that was strong enough to hold three women sitting on it. I wanted this rack to be just as sturdy."
“That’s a good tagline,” I joked. “Holds three women.”
“Strong enough for the whole family,” he quipped back.
“Men on the internet”: a designer’s story
Engaging with the community for feedback was a new experience for Matt. "This was the first time I formally sought community feedback," he shared. "Some of the comments were a bit…let’s call them rough around the edges.”
“Well, you’re dealing with men on the internet,” I said.
“Exactly,” he laughed. “But I focused on the intent and content of their feedback. Most of the design ideas were really good. For example, someone suggested adding round holes in the sides, which actually looked way better."
The community's color preferences also influenced the final design. "People had varied tastes—many liked Scandinavian light color, while others preferred walnut. It was interesting to see the different opinions on color. I decided on a natural, clear oil finish, which aligns with the Scandinavian look that I prefer. Someone even wanted it in orange, which is right up my alley, but maybe too bold for most people."
Feedback on practical aspects of the design was equally valuable. "One comment suggested using cable ties and/or Velcro for wire management—that was a brilliant idea, so I implemented it. Another suggestion was to hide the wires, which I also incorporated into the final design.”
“Overall it sounds like a very symbiotic relationship between you and the community,” I said.
“Absolutely,” he said. “Most everyone provided excellent feedback, some of which was really positive and even very beautiful in their words.”
Cutting costs without cutting corners
Maintaining high-quality manufacturing while managing costs was a major challenge for Matt. "I have a high-precision CNC machine, which is quite expensive. Producing top-notch quality is something I can handle, but material costs are substantial," he explained. "We decided to switch to 100% Baltic birch for the back panel, which is the largest piece. But we reduced costs elsewhere, like getting rid of the vibration damping in the bottom shelf, so things evened out quite a bit.”
Sketch, cut, mount
“What’s the best part about the design process?” I asked.
"I love the initial sitting down with my big German sketchbook,” he said. “It starts neat and then becomes a huge mess with notes everywhere. Designing on the computer is magical—cutting a part out and seeing everything fit together perfectly (after the third try). There's something satisfying about putting something on the wall and seeing it up there. Live with it for a while and let it talk to you.”
However, the journey was not without its challenges. "There are times—somewhere in the prototype phase—when I start feeling uncomfortable and doubt myself, wondering if it’s going to work or go anywhere. The mounting overhead costs also adds to the stress. When that happens, I need to step away and go jogging. It helps clear my mind. Then I have other production work to do, which is grounding and brings me back to a place of confidence."
Advice for Aspiring Designers
“Any advice for aspiring designers?” I asked.
"Be open to feedback. Everyone has an idea. It can be shocking how good some ideas are. Keep ego out of it and be willing to learn from others. If something intrigues you and keeps coming back to you at odd moments, that’s something you should work on. And if it’s fun, that’s even better."
Reflecting on the process, Matt said, “It’s been really nice to go through this. People are open. I feel like I doubt myself more than the people I’m working with doubt me. That’s encouraging.”